Production infrastructure data integration system
Challenge
A car parts manufacturer needed a system that would integrate data from production lines and advanced production control systems. The new solution was to help monitor the part’s production path and thus help better manage product quality. In the case of a possible malfunction, the system was to enable the cause of the abnormality to be found quickly.
Fabrity faced the task of integrating data from multiple production systems using different data standards. The creation of the new tool required an in-depth understanding of the entire production process and the collection of information on all systems previously used in it.
The various production systems are supplied and serviced by different suppliers. The project not only required excellent data integration skills. It was also necessary to possess very good communication skills and to reconcile the interests of multiple parties, as well as to make project management methodologies consistent between entities. To this end, a number of workshops were held with the customer and with suppliers.
Industry
Key point
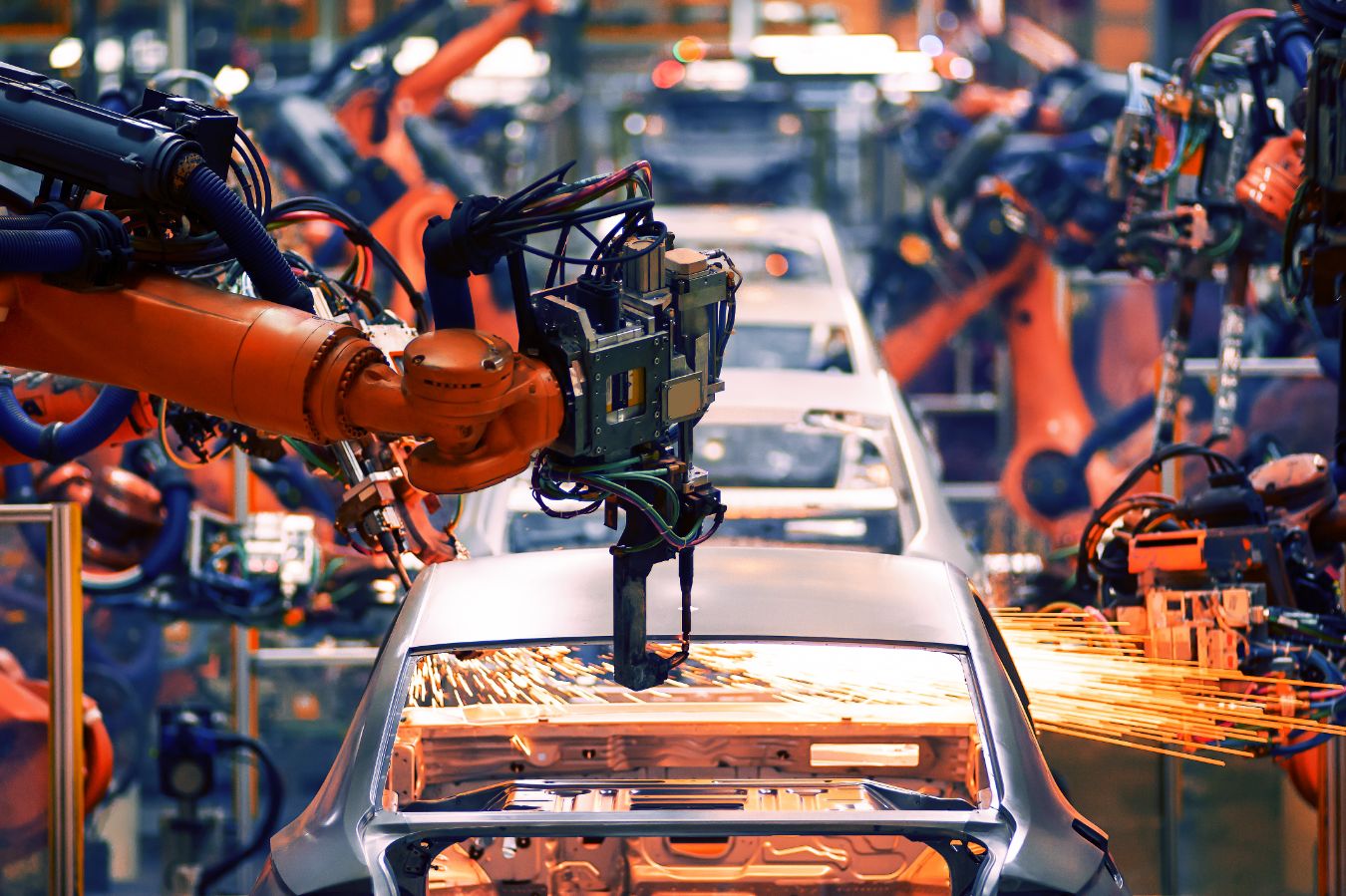
Why Fabrity?
Solution
A system has been created that collects data from various sources, integrate it and creates a data warehouse. The solution combines data from the old production control systems and the SAP system with an additional link to the MES class system (production execution system).
The system, developed by Fabrity, allows parts to be searched for on machining lines, assembly lines, finished parts warehouses and in products shipped to customers.
Factory managers, with the help of the search engine created, can easily and intuitively find data collected in one source. It is a personalised solution that meets all the requirements the client has put forward.
Results
The system was developed and implemented within 9 months. At the time of its creation, hybrid teams operated. The development team and Scrum Master from Fabrity worked closely with Product Owners and the Project Manager on the client-side. The work followed Scrum guidelines based on direct and continuous contact with the client. This way of working together allowed Fabrity’s experts to understand the customer’s needs very well and create a tailored solution.
A key customer benefit of implementing the new system is the streamlining of the reverse parts search process by reducing information search time. Searching for data is possible with the help of a single search engine based on an integrated and consistent data source, instead of several independent sources as before.
- Integrated data from 20 legacy tools and databases
- Monitors millions of parts whose data are processed in the system
- Has about 50 complex search criteria available in 4 independent search engines
- Presents search results in a unified and aggregated way
- Improves production supervision
- Collects historical data